Putting Drone Technology to the Test
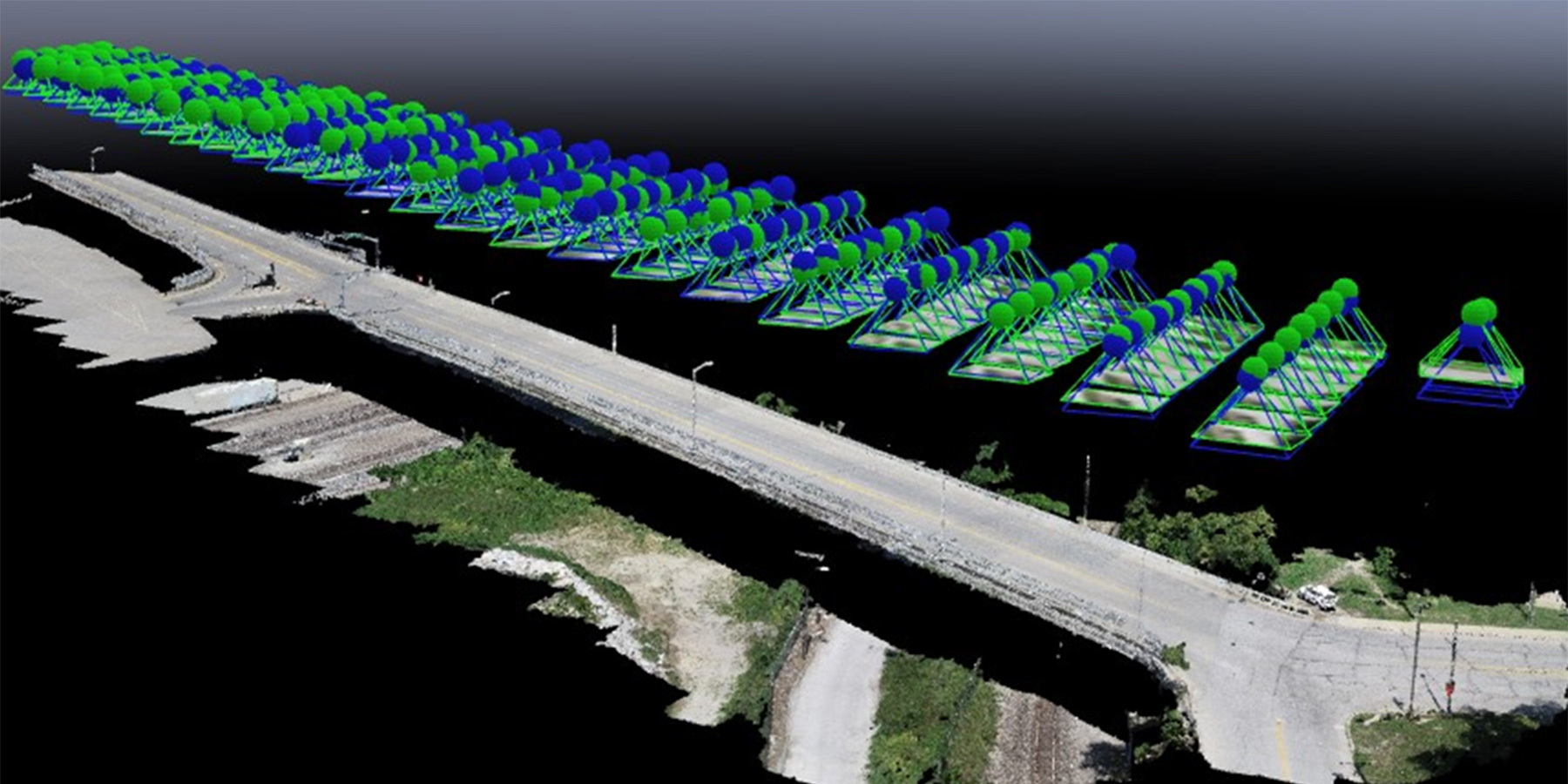
While drones have long captivated aviation enthusiasts and solicited curious finger pointing from onlookers, advances in the technology are leading AEC industry professionals to explore their ability to save time and money on infrastructure projects.
Benesch Technical Manager Bret Tremblay is actively exploring the benefits and untapped potential of drone usage throughout the industry. In the below article, Bret shares how he’s putting drones to the test in the field.
Meet Our Expert
America’s infrastructure is aging—it’s no secret—and with this aging comes the need to be able to inspect structures efficiently and safely. While the boots-on-the-ground approach is a tried-and-true method, advances in drone technology have led me and many others to rethink how we approach the inspection, maintenance, and analysis of our infrastructure. An especially promising approach is the use of thermal drones to better detect concrete delamination on bridge decks or parking garage top decks.
Since a delamination is difficult to detect with the naked eye, inspectors typically utilize concrete sounding techniques. While manual sounding techniques can yield accurate results to experienced inspectors, external variables including adjacent traffic or ambient noise, roadway debris, and very minor pockets of delamination can be challenging to identify.
A thermal drone evaluation involves flying a drone, equipped with a thermal camera, over a bridge deck to identify areas of varying temperature. The temperature variation is attributed to the difference in thermal conductivity of pockets of the deck void of concrete in comparison to areas adjacent to that that are non-delaminated of intact concrete deck. As the ambient air temperature heats up, pockets of delamination within the concrete heat up much faster than the rest of the deck resulting in locations that are slightly warmer than surrounding non-delaminated areas, typically we see this temperature variation between 2°-12°.
Using the drone footage, we can isolate the temperature variations and provide the specific location and size of the potential delamination. This results in an objective, non-biased, repeatable, quantifiable evaluation not subject to individual human interpretations.
A Head-to-Head Comparison
A project for Sedgwick County Public Works in Kansas gave us the opportunity to put the thermal technique to the test with a head-to-head comparison between sounding devices and thermal imaging. The 63rd Street South over the Arkansas River—a nine-span, prestressed concrete, double tee beam structure built in 1979—needed an in-depth inspection. A thermal drone deck scan was performed by Benesch drone pilots concurrently with the up-close inspection to identify possible areas of delamination within the concrete deck.
Prior to the scan, Benesch inspectors, using concrete sounding techniques, identified areas of presumed delamination with spray paint for comparison purposes.
Sounding techniques indicated delaminated areas in 1.86% of the approach slabs and 0.38% in the deck for a total of 35 individual delaminated areas. The thermal process indicated delaminated areas in 2.20% of the approach slabs and 0.29% in the deck with 45 individual delaminated areas. What these results told us was that the deviation in accuracy between conventional sounding and thermal was within a tolerance level we were comfortable with. But most importantly, the thermal was able to identify more areas of delamination that were so small that the sounding didn’t pick up.
Just like going to the doctor and getting treatment for a person’s health condition early, these small areas we are able to detect with thermal are the start of a future problem. Early identification allows our clients to put together data-driven decisions in their maintenance program sooner to eliminate more extensive repairs in the future.
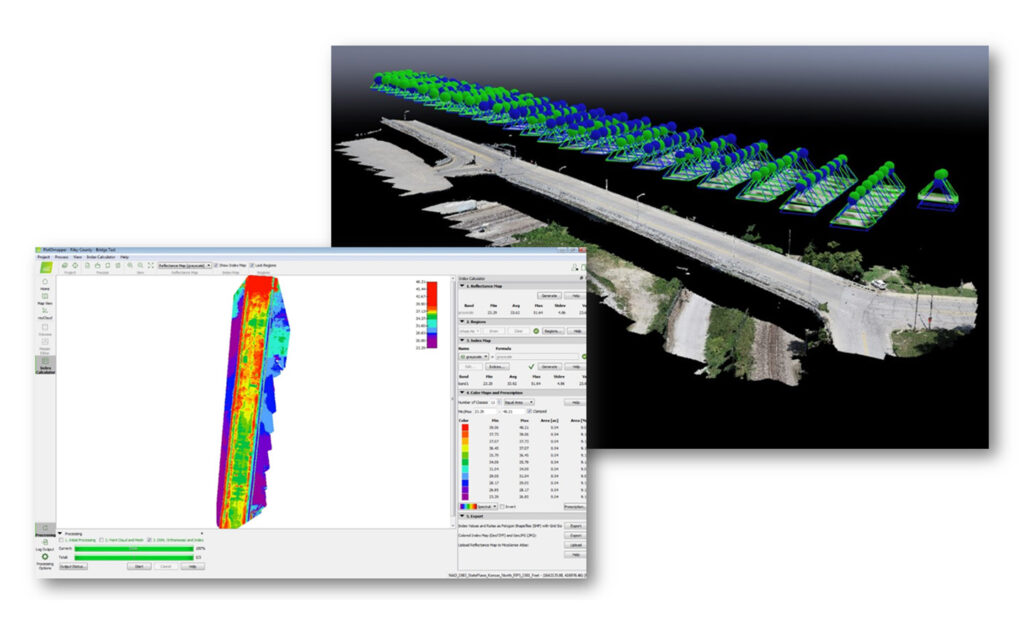
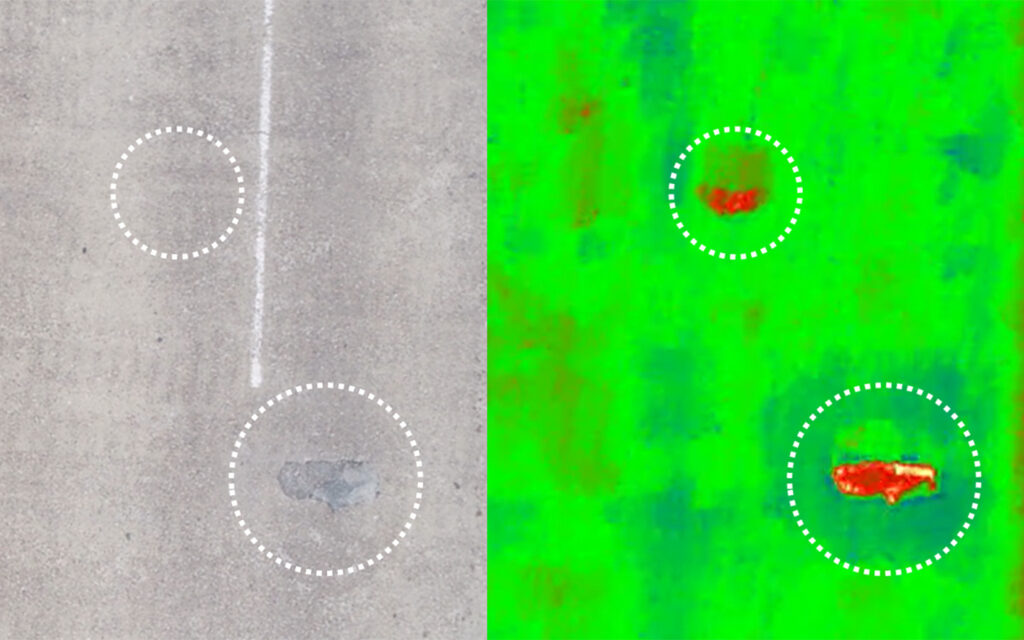
The thermal inspection took 35% less time and cost 36% less than the sounding method. Overall, we were pleased to see that the thermal inspection yielded results with a reduction in work hours and cost.
While these results were expected, it was nice for both the Benesch team and the client to see the side-by-side comparison. Further, our success in this instance encourages us to continue exploring what can be done with drones and other technologies starting to make waves in the industry by supplementing traditional procedures with innovative thinking.
Follow Benesch on LinkedIn for the latest news and insights from our experts.