Innovative Delivery Method a Success on I-240
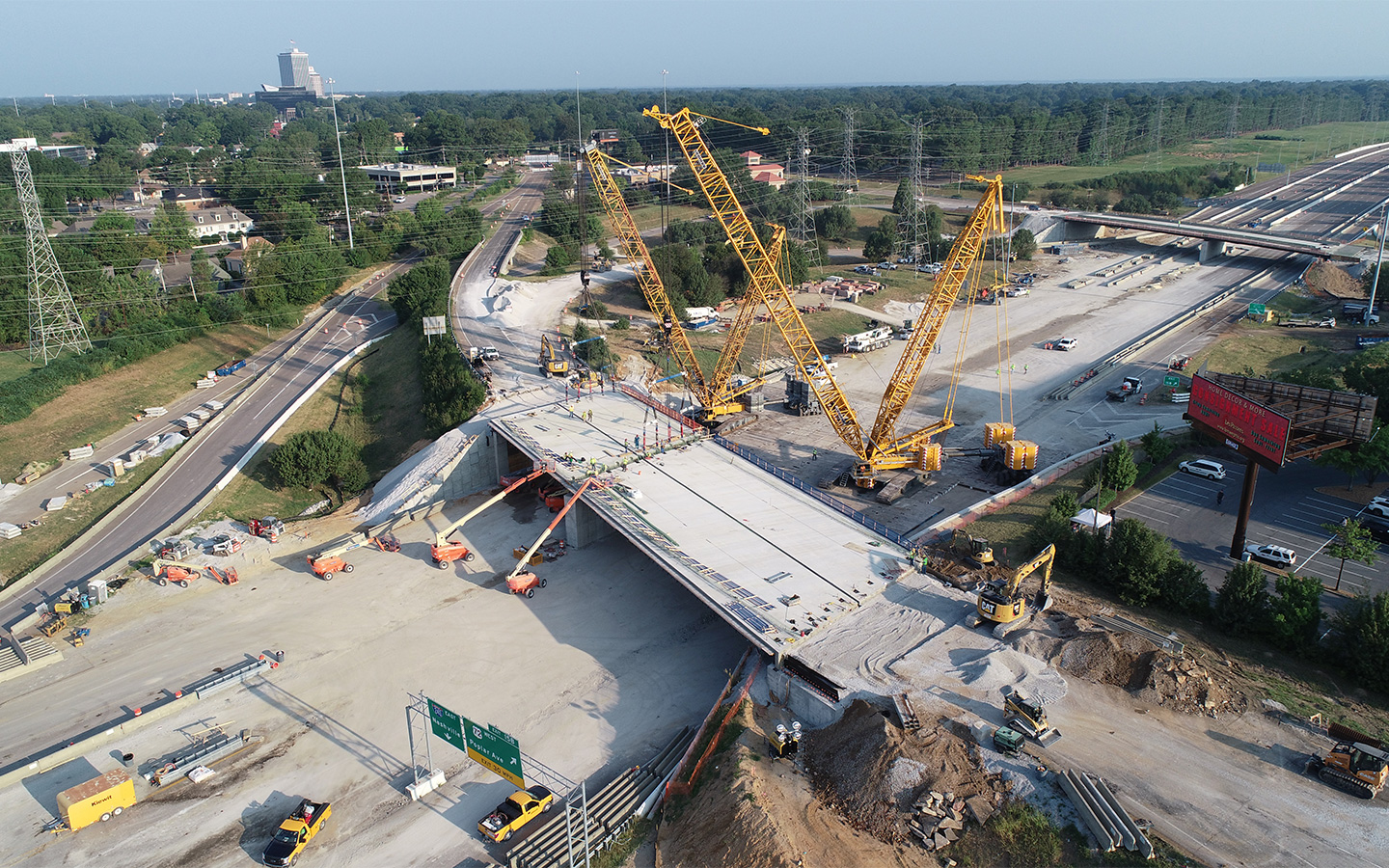
MEMPHIS, TN — When the Tennessee Department of Transportation (TDOT) was faced with replacing or repairing four deficient structures at the Poplar Avenue interchange as part of further widening on I-240, they sought an innovative delivery approach that would cut construction time.
Regional seismic conditions, compounded with traffic levels of approximately 180,000 vehicles and 20 freight trains each day, made it clear that the project—dubbed MemFix 4—would require complex engineering solutions in order to be completed quickly and minimize impacts to travelers.
TDOT chose the Construction Manager General Contractor (CMGC) delivery method as the preferred approach to accomplish the project.
The I-240 corridor, which curls around eastern Memphis, TN, and connects motorists to the Memphis International Airport, has been under nearly constant construction for several years to meet increasing traffic demands.
Implementing CMGC
Benesch began working with the Department on MemFix 4 in 2015. A technical study was completed not only to define the scope of the project and its probable costs, but also to determine the viability of utilizing CMGC.
CMGC maximizes efficiency and enables close collaboration between the project owner, design team, and contractor while facilitating effective use of Accelerated Bridge Construction (ABC) techniques to further expedite the construction process. More traditional design delivery methods such as design-bid-build could have easily required three years to construct the project. By combining the CMGC delivery method with ABC techniques, Benesch and TDOT believed MemFix 4 could be completed in half that time.
Innovative Methods and Materials
Innovative construction methods and materials made all the difference for MemFix 4. From 26,000 linear feet of micropiles to new substructures constructed under traffic and modular superstructures rolled and lifted into place, each of the four interchange structures presented unique opportunities for innovation.
East and Westbound Poplar Avenue
The four- and five-span PPC beam Poplar Avenue bridges were replaced with two-span steel girders in order to satisfy seismic codes and improve long-term corridor reliability and flexibility. Replacing the existing concrete structures with steel also allowed for modular construction techniques.
While the new substructures were constructed without impacting use of the existing bridges, the superstructure units were all built off-site at a “bridge farm” two miles away. Once the substructures were ready, the bridge units were rolled down I-240 using Self-Propelled Modular Transporters (SPMTs). Custom steel bearings and framing elements allowed for the transfer of seismic loads while meeting rapid ABC demands. The existing bridges were demolished, and the modular superstructure units were lifted into place using two crawler cranes.
Each replacement occurred during 56-hour closure weekends of I-240— significantly less time than if the bridges were phase constructed in place.
WATCH – TDOT captured the replacements using time-lapse video. See WB Poplar Ave. here; EB here.
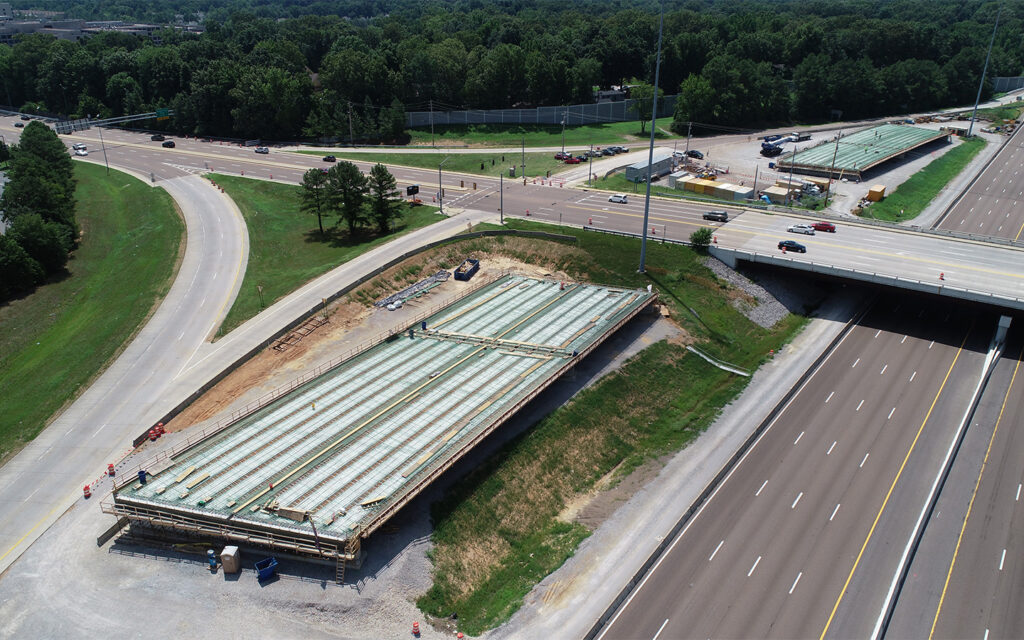
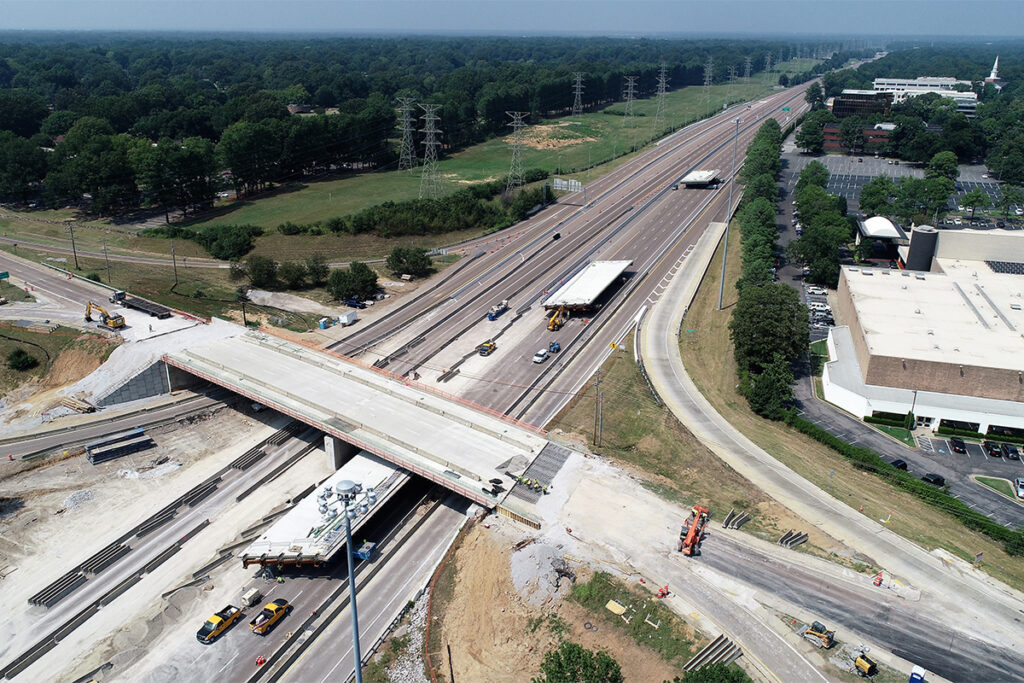
Norfolk Southern
The Norfolk Southern (NS) Railroad corridor required continuous operation of two tracks, allowing only two 12-hour interruptions to a single track at a time. To replace this bridge, a temporary shoofly structure was constructed adjacent to the existing bridge. It was comprised of temporary concrete piers supported by micropile foundations to minimize ground disturbance. The permanent steel superstructure supporting a ballasted track was erected on the shoofly alignment.
With trains traveling on the shoofly structure, the old bridge was demolished, and the new substructures were built. The two new, 2.2-million-pound superstructure sections were then slid 35 feet into place, one track at a time, during two weekend interstate closures—an engineering first on an active railroad bridge in Tennessee.
WATCH – TDOT captured each weekend slide-in using time-lapse video. See the first slide-in here, and catch the second one here.
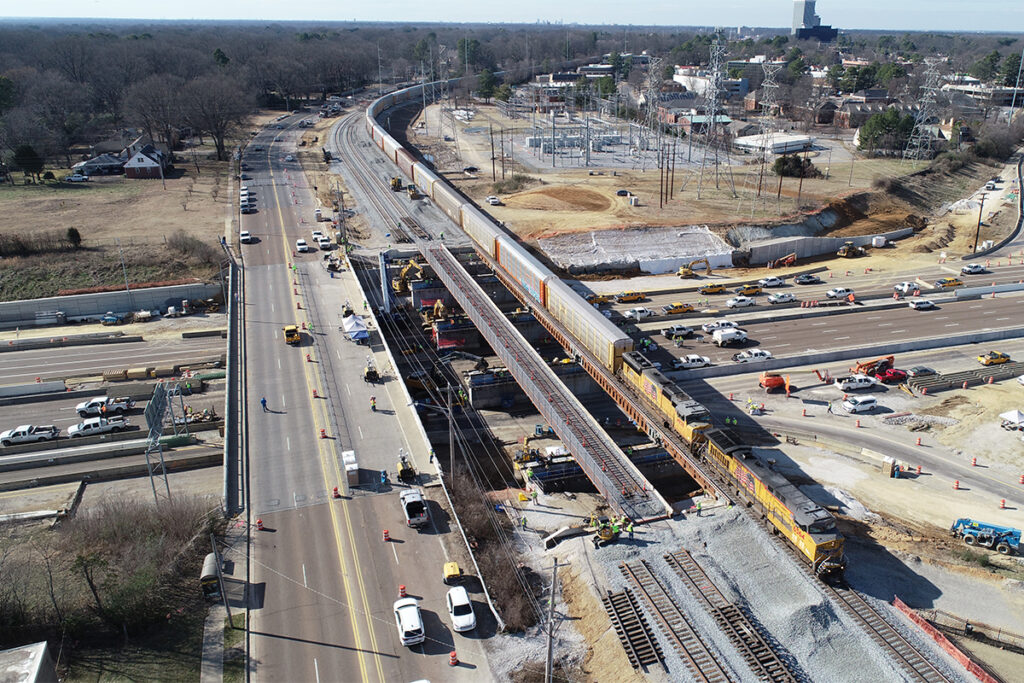
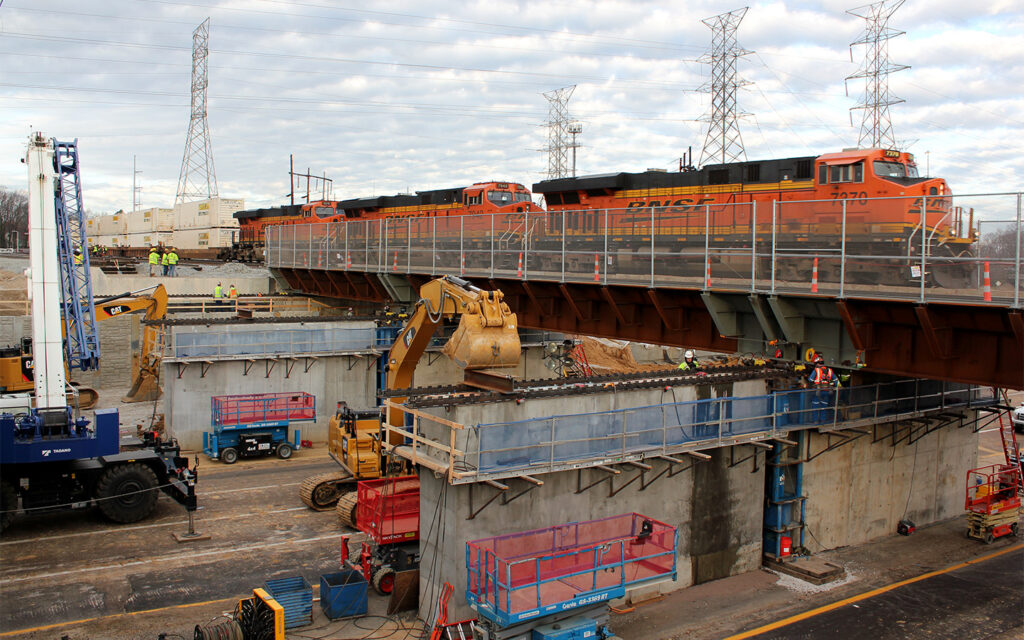
Park Avenue
The Park Avenue bridge was preserved using novel foundation retrofit design. Finite element modeling fine tuned the bridge’s seismic behavior, which optimized the use of micropile retrofits and minimized materials and cost.
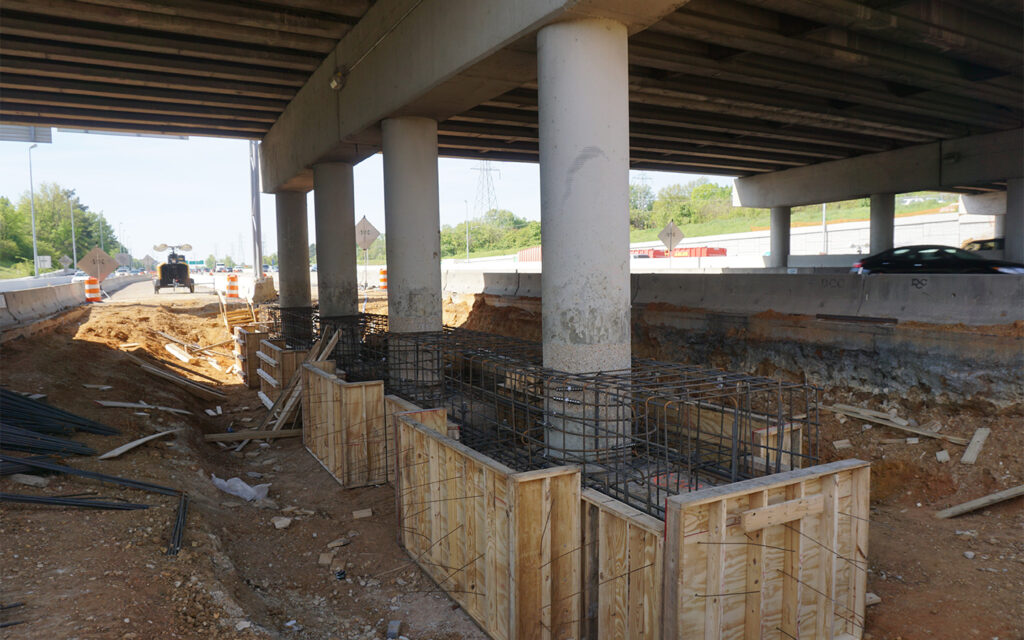
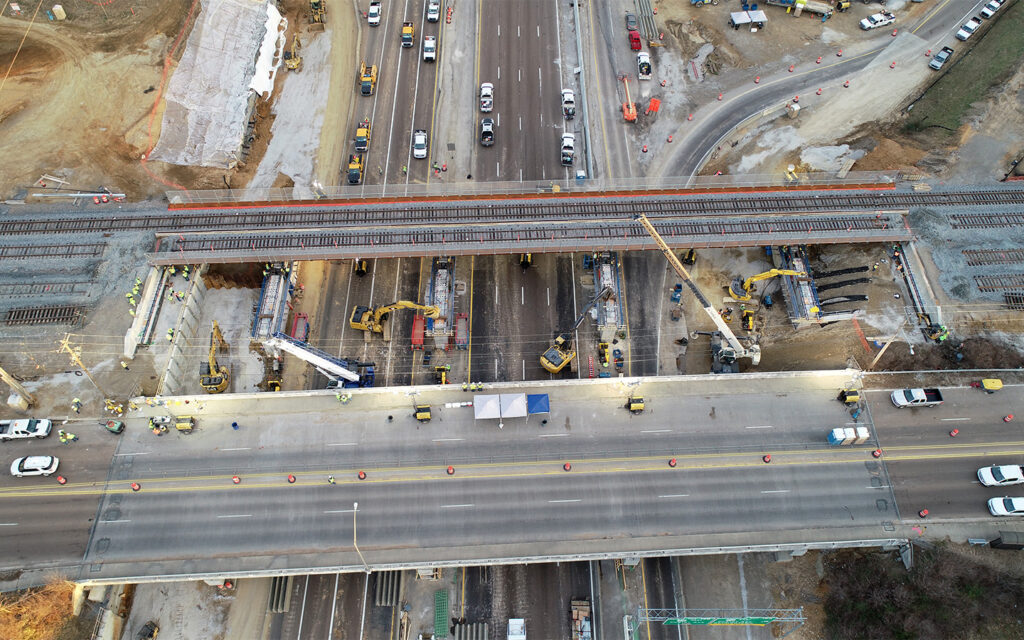
Project Success
Concurrent to the start of design work in September 2016, Kiewit Infrastructure South Co. was selected as the Construction Manager (CM) for the project. Benesch, Kiewit and TDOT worked collaboratively on the project’s design and continued their partnership through the construction phase. The design phase was completed in October 2017, with construction activities beginning in January of 2018.
In total, 18 months were shaved off the project’s construction schedule while reducing impacts to vehicular and rail traffic, thanks to CMGC and ABC techniques. Lane closures on I-240 started the first week of January 2018, with all original lanes opened again to traffic by the third week of December—just under 12 months later.
The project also resulted in minimal change orders at a significantly lower level than the industry average – especially on a project of this size.
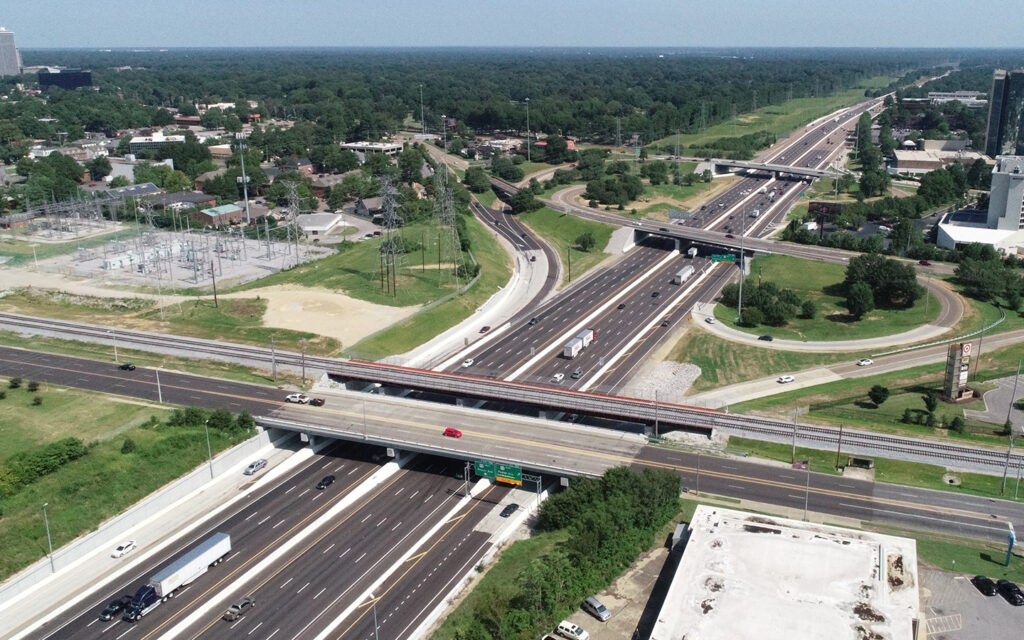
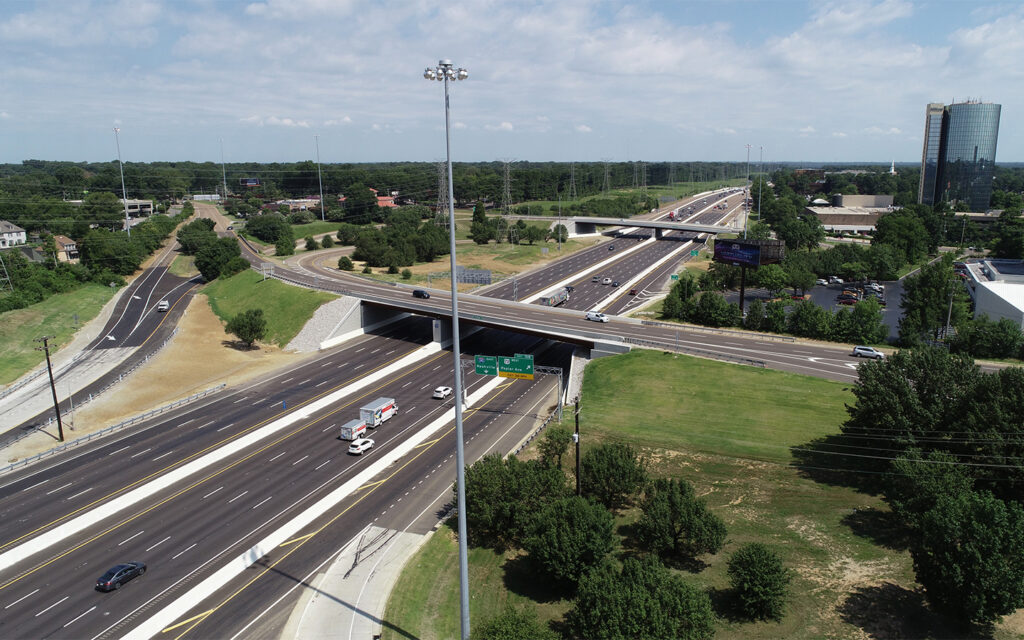